What is Process Automation?
Drive the expansion of process automation in your company with integration.
Introduction to process automation
In today's fast-paced and competitive world, organizations are continually seeking ways to streamline their operations and improve productivity. This SEEBURGER guide to process automation explores a diverse range of automation use cases across industries such as financial services, manufacturing, retail and automotive. From streamlining repetitive tasks and data entry processes to facilitating data analysis and decision-making, automation technology is transforming traditional workflows and offering new avenues for growth.
Above all, this guide seeks to provide actionable insights and guidance for organizations considering the adoption of automation technology. Whether you are a small startup looking to scale operations efficiently or a large enterprise seeking to drive digitalization across your organization, this page will serve as a valuable reference, equipping you with the necessary knowledge to make informed decisions, tap the potential of business automation and embrace automation technology as a means to optimize the workforce and foster innovation.
Four types of process automation
RPA (robotic process automation), BPA (business process automation), DPA (digital process automation) and IPA (intelligent process automation) are different types of process automation that aim to make complex business and production operations more effective and efficient by automating tasks. Each type offers the primary benefits of increased efficiency, lower costs and reduced errors, while the main difference between each type of process automation is the level of integration.
What is robotic process automation?
RPA is the use of software robots or "bots" to automate repetitive tasks, streamline workflows and increase efficiency. RPA software executes specific rules-based tasks and eliminates the need for manual repetitive and tedious tasks, allowing humans to dedicate their efforts to more impactful tasks and higher-value work. For example, RPA in the manufacturing and automotive industries has resulted in the use of robotic arms to effortlessly assemble intricate components, reducing human error and increasing throughput.
What are examples of robotic process automation?
Several examples of business applications of RPA include:
- Data entry: Bots can extract data from various sources such as spreadsheets, emails and documents, and automatically enter it into relevant systems or databases. Automating your bookkeeping is a good place to start your company’s digitalization journey while reducing manual errors and freeing up human resources for more complex tasks.
- Invoice processing: Instead of manually entering invoice information into accounting systems, RPA bots can scan and extract data from invoices, perform validations and update the necessary financial records. This speeds up the process and reduces errors.
- Customer service: Chatbots powered by RPA can handle customer inquiries, answer frequently asked questions and assist with basic troubleshooting. They can also provide instant responses, saving time for both customers and support staff.
- Report generation: Bots can retrieve data from multiple sources, consolidate it, and generate reports automatically. This eliminates the need for manual data gathering and manipulation, allowing for faster and more accurate reporting.
- HR onboarding: RPA bots can assist with employee onboarding processes by automatically creating accounts, generating paperwork and sending out welcome emails. This reduces administrative overhead and ensures a smooth onboarding experience.
- IT support: Bots can perform basic IT tasks like password resets, software installations and system updates. This helps organizations resolve common IT issues quickly, reducing the workload on support teams.
RPA can be applied to many other areas where repetitive rules-based tasks are involved, enabling organizations to improve productivity, accuracy and scalability.
What are the benefits of robotic process automation?
RPA offers many business benefits, making it a valuable automation solution for organizations to:
For more information about how to optimize and manage your enterprise workflows with SEEBURGER SAP capabilities and easily integrate workflows into any SAP ERP system, read our blog “Workflow Management Made Easy."
What is business process automation?
Gartner describes business process automation (BPA) as the automation of complex processes and functions that “run the business” as opposed to the tasks that “count the business.” Its primary purpose is to enhance operational efficiency, reduce manual efforts, and improve overall productivity so that employees can focus on more strategic and value-added activities.
BPA requires some programming to leverage its capabilities, such as reporting and custom workflows, because it requires knowledge of databases, middleware platforms and scripting languages.
Business process management lifecycle
With the Business Process Management (BPM) lifecycle, automation initiatives can be implemented incrementally in cyclical phases to reduce the concentrated workload of the above activities, from programming to documentation, reducing the workload on staff. The BPM lifecycle is therefore an orderly and continuous approach to process optimization and automation.
- In the first phase, process identification, the key processes that contribute significantly to a specific problem are identified. It's important to consider the interdependencies between individual processes, as it's usually not just one process that is affected, but a group of processes. The phase concludes with an updated or entirely new process architecture.
- During the process assessment phase, a detailed and realistic current process model is created to accurately identify which process components are causing the problem. The accurate process model must align with employee perceptions and serves as the basis for effective communication, whereby Business Process Model and Notation (BPMN) can be used to establish a common language.
- In the course of process analysis, key metrics are identified to quantify and evaluate processes based on current process models. Initial solution approaches are developed and relevant metrics are documented. The goal is to create a prioritized list of root causes for the identified problems, organized by urgency and feasibility along with initial solution suggestions and relevant metrics for future evaluation.
Process mining supports the analysis phase:- Process analysis at the level of individual tasks and resources
- Data-driven approach that uses facts and figures based on event log data for analysis, rather than mere assumptions
- Existing processes and their potential for optimization and deviations between model and reality are revealed, so that models can be adapted, corrected and improved, resulting in accurate and realistic process models that provide an undistorted representation of reality
- In the process optimization phase, a target process model is created that specifically addresses the weaknesses of the current situation. Since there are many different improvement options, a careful assessment of benefits and costs is required to set priorities. It is important to keep in mind that new approaches and optimization methods may bring new challenges. The goal at the end of this phase is to select a solution or combination of solutions that most effectively addresses the problem while minimizing unwanted side effects.
- During process implementation, the current process is replaced by the target process, and the dependencies of the individual processes must be taken into account.
- Effective change management is essential. In particular, organizational change management prepares employees for the upcoming changes. In practice, this means adapting existing working methods to new processes. Resistance to change can be minimized through early involvement and effective, positive and transparent communication.
- Another key topic is process automation. With the help of BPA and RPA, IT systems are used to fully automate (sub)processes or to provide automation tools that support employees in their tasks. With each cycle run, more components of the processes can be gradually automated, resulting in cost savings, less susceptibility to errors and higher customer satisfaction.
- Finally, process monitoring completes the lifecycle. Even optimized processes require ongoing monitoring and evaluation. Metrics are used to measure results against the previously defined goals of the initiative. Over time, new challenges may arise or the requirements for the process may change. In such cases, the processes must be adapted in an agile manner to ensure continuous optimization and to achieve long-term maximum results and efficiency. If necessary, a new cycle run is initiated.
This structured approach, along with the cyclical nature of the projects, allows for a clean and thoughtful implementation of process optimization and automation. Below are some practical use cases for business process automation.
What are examples of business process automation?
Five popular examples of business process automation include:
- Workflow automation: With workflow management systems, businesses can easily automate repetitive and manual tasks. For instance, they can use drag-and-drop features to create workflows that automatically route documents for approval or notify team members about specific actions required, from submitting annual leave to submitting travel expenses. This streamlines processes, saves time and reduces the likelihood of errors.
- Customer service automation: BPA tools enable businesses to automate customer service processes, such as handling common inquiries or providing self-service options. Through chatbots or AI-powered virtual assistants, customer queries can be addressed 24/7, improving customer satisfaction and allowing human agents to focus on more complex issues.
- Reporting and analytics automation: Integration platforms can automate the generation and distribution of reports and analytics. Companies can create dashboards, set up scheduled reports and automate data analysis, enabling data-driven decision-making and real-time insights.
- ERP process automation: Enterprise resource planning (ERP) systems integrate various functional areas of a business, such as finance, human resources, supply chain and manufacturing. By automating tasks and workflows within an ERP system, organizations can enhance communication, eliminate errors and increase data accuracy. This enables faster decision-making and enables organizations to adapt to changing market demands more effectively.
- Compliance automation: BPA supports regulatory compliance by standardizing processes and providing audit trails. By implementing automated workflows for regulatory compliance purposes, businesses can ensure adherence to legal requirements, standards and procedures. Automated workflows simplify and expedite processes such as document management, auditing, reporting and record-keeping, allowing businesses to proactively meet regulatory obligations. BPA enhance increases transparency, traceability and compliance accuracy, thereby reducing risks and potential penalties.
What are the benefits of business process automation?
Business process automation ensures that organizations can streamline operations without requiring extensive coding knowledge and empowers teams to quickly build and optimize business processes.
BPA offers organizations four key benefits:
For more information about how to optimize and manage your enterprise workflows with SEEBURGER SAP capabilities and easily integrate workflows into any SAP ERP system, read our blog “Workflow Management Made Easy."
What is digital process automation?
Digital process automation (DPA) refers to the use of technology to streamline and automate organizational processes. It involves the design, implementation, and management of digital workflows, allowing businesses to reduce manual efforts and increase operational efficiency. DPA typically integrates various tools and technologies, such as artificial intelligence, robotic process automation, and data analytics, to automate repetitive tasks, gather insights, and drive decision-making. By automating processes, DPA helps businesses save time, reduce errors, and enhance productivity.
What are examples of digital process automation?
A range of use case examples for digital process automation (DPA) include:
- Invoice processing: Similar to RPA, DPA can streamline invoice processing and approval workflows. Instead of manually entering data from invoices into accounting systems, automation software can be used to extract data from invoices, verify the information and automatically update the necessary systems. This not only saves time and reduces the risk of errors but also improves efficiency by eliminating the need for manual data entry.
- Customer onboarding: Customer onboarding is a critical process for businesses, but it often involves repetitive tasks such as data collection, verification and documentation. Digital process automation can simplify this process by using software to automate data collection from customers, perform necessary background checks, generate required documents and trigger follow-up actions like sending confirmation emails. By automating these tasks, businesses can enhance the customer experience, reduce the time required for onboarding and increase operational efficiency.
- Blockchain technology: The role of blockchain in digital process automation includes conducting safe and secure transactions with cryptocurrencies. Blockchain technology in banks can make it easier to fulfill and document regulatory requirements, contracts and loan applications by enabling more comprehensive and secure verification processes. With blockchain technology, you can seamlessly trace the steps in any data transactions.
These automation use case examples demonstrate how DPA can optimize various business processes while improving productivity and customer satisfaction.
What are the benefits of digital process automation?
Digital process automation offers numerous benefits to businesses. Here are the top five:
DPA empowers businesses to achieve operational excellence, improve customer satisfaction, reduce costs and drive innovation, ultimately leading to increased profitability.
What are examples of intelligent process automation?
Examples of IPA, combining RPA and AI to enhance and automate business processes, include:
- Data entry and extraction: IPA can automate data entry and extraction by using optical character recognition (OCR) techniques to read and extract information from documents, such as invoices or forms. This eliminates the need for manual data entry, reduces errors and saves time.
- Customer service: IPA can be used to automate responses to common customer inquiries. Chatbots powered by AI can handle basic customer queries, freeing up human agents to focus on more complex issues, improving response times and enhancing customer satisfaction. In the retail industry, customer service chatbots provide instant and personalized assistance, improving the shopping experience and driving customer loyalty. Read our blog to learn more about the importance of intelligent systems integration in e-commerce.
- Fraud detection: IPA can assist in identifying and preventing fraudulent activities. By analyzing patterns and anomalies in data, AI algorithms can detect potential fraud in financial transactions, insurance claims, or online activities. This helps organizations proactively address and prevent fraud, saving money and protecting their reputation.
- Supply chain management: IPA can optimize supply chain processes by automatically tracking inventory levels, monitoring demand fluctuations and predicting supply chain disruptions. This enables businesses to maintain optimal stock levels and improve efficiency in the supply chain. Integrated retail inventory management systems, for example, can be used to automate stock monitoring, replenishment and pricing to ensure optimal product availability.
- Invoice processing and accounts payable: IPA can automate invoice processing by extracting relevant information from invoices, verifying invoices against purchase orders and initiating payment processing. This eliminates manual data entry, reduces errors and accelerates the accounts payable process.
- Workflow automation: IPA can automate workflows by intelligently routing tasks and documents to the appropriate individuals or departments. By analyzing process inputs and criteria, IPA can automate approval processes to improve efficiency and reduce bottlenecks.
What are the benefits of intelligent process automation?
IPA offers many benefits to help business stay competitive, including:
RPA vs. BPA vs. DPA vs. IPA
What are the advantages of using one type of process automation over another?
RPA vs. BPA
RPA is generally used for solving problems at the task level, while BPA is used for solving problems at the process level. According to Gartner 1, “RPA should be used as the last resort for automation when there is no API available and there is a requirement for simpler workflow execution.”
- RPA does not have intelligence or decision-making capability unless it’s combined with AI and machine learning.
- RPA is ideal for automating repetitive tasks that do not require a reengineering of existing systems to improve productivity and reduce costs.
- BPA is best suited for large automation projects that require integration with other applications and data sources.
- BPA is ideal for automating workflows and tracking workflow progress using cloud services.
1Gartner, “Quick Answer: How to Choose the Right Use Cases for Robotic Process Automation,” Annie Garcia, 2022
BPA vs. DPA
Business process automation (BPA) and digital process automation (DPA) are both valuable tools that can optimize processes within an organization. While they share similarities, there are distinct differences in their use cases.
BPA focuses on automating repetitive human tasks and workflows within an organization. It aims to enhance efficiency, reduce errors and save time. BPA is often used in areas such as:
- Administrative tasks: Automating tasks like data entry, document management and scheduling can free up valuable time for employees.
- Human resources: BPA can automate the employee onboarding process, performance evaluations and time management.
- Customer support: Automating ticket routing, responses and basic customer inquiries can improve response times and enhance customer satisfaction.
- Finance and accounting: BPA can streamline approval processes like invoice processing.
DPA focuses on automating end-to-end digital processes that involve both humans and systems. It not only streamlines tasks but also enables seamless collaboration and integration across various tools and platforms. DPA is commonly used in areas such as:
- Customer experience: DPA can automate online sales processes, personalize marketing campaigns and analyze customer feedback, enabling organizations to deliver exceptional customer experiences.
- Supply chain management: By automating inventory tracking, order fulfillment and logistics, DPA helps organizations optimize their supply chain and gain real-time visibility into the process.
- Compliance and risk management: DPA can help companies ensure reliability compliant IT security with automated compliance monitoring, regulatory reporting and risk assessments, ensuring they stay compliant and reduce the chances of costly errors or penalties.
- Product development: DPA can be used to automate the collection and maintenance of product information, product design workflows, collaboration among cross-functional teams and quality assurance processes, enabling faster time-to-market and improved product quality.
In summary, BPA focuses on automating repetitive tasks and workflows, while DPA goes beyond that by digitalizing and optimizing end-to-end processes, enabling better collaboration and integration. Both BPA and DPA have their unique use cases, and organizations should evaluate their specific needs and requirements to determine which approach to automation best suits their goals.
At times, selecting a single process automation type might not effectively address intricate challenges. In such cases, IT teams and business decision-makers may choose a more comprehensive strategy, combining and integrating various automation efforts. Hyperautomation represents this holistic approach, encompassing the entire lifecycle of automation. The distinction between traditional automation and hyperautomation lies in their scope and emphasis. Automation is a broad term for utilizing technology to execute tasks without human intervention, whereas hyperautomation specifically underscores the integration and orchestration of multiple automation initiatives, tools and technologies to develop a holistic and sophisticated solution.
Use cases for process automation
Process automation is where efficiency meets innovation. Across various industries, organizations are leveraging the power of automation with data transfers, onboarding, API testing, onboarding, and the Industrial Internet of Things (IIoT) to streamline operations, improve productivity, drive growth and enhance the customer experience.
Data transfer automation
Data transfer automation involves transferring data files, documents or other information from a source to a destination, without manual intervention. It involves setting up pre-defined rules, workflows or schedules to initiate and manage data transfers.
Automated data transfer using MFT offers benefits such as increased productivity, enhanced data security, improved reliability and reduced operational costs. It allows organizations in the financial services industry, for example, to handle large volumes of data transfers efficiently and ensures that data is moved reliably and securely between systems.
API testing automation
API testing automation plays a critical role in the business world, particularly in the financial services and automotive industries. These industries heavily rely on APIs to connect various systems and enable communication between applications, making API testing automation a vital component for ensuring the reliability, accuracy and security of these interfaces.
In the financial services industry, APIs are typically used to enable secure and efficient transactions, provide real-time account information and offer corporate digital services for cash management. APIs also play a crucial role in “open banking,” in which banks and other financial institutions allow third-party developers to securely access customer data with the consent of account holders. By opening up their APIs, banks provide opportunities for innovative fintech companies, mobile apps and other financial service providers to create new products and services that improve the banking experience for customers. With API testing automation, business units within the bank can ensure that transactions are executed accurately, validate data integrity and promptly identify and resolve any issues before they impact the corporate customer experience or compromise financial information.
Similarly, the automotive industry relies extensively on APIs for various critical functions such as vehicle diagnostics, remote application control, software updates and integration with third-party services like navigation and entertainment systems. API testing automation in the automotive industry helps manufacturers and service providers ensure the seamless integration of these APIs and guarantee the performance, reliability and security of connected systems. By automating the API testing process, automotive companies can quickly identify bugs or compatibility issues and shorten product development cycles while delivering more robust and secure applications to their customers.
Onboarding automation
Partner onboarding, customer onboarding and employee onboarding can be automated and tailored to specific industries, simplifying the process of bringing new people onboard and fostering successful collaborations. For example, use cases in the retail and financial services industries for automated onboarding of partners, customers and employees include:
Retail industry use cases
- Customer and partner onboarding: A retail company can use automation to streamline the onboarding process for new suppliers, distributors, vendors and customers. This includes automated contract generation, automated account creation, digital document sharing and signing, self-service sign-up options, personalized welcome messages and tailored product recommendations based on customer preferences.
- Employee onboarding: Automation can help retail companies streamline employee onboarding processes, such as automating the creation of employee accounts, distributing onboarding materials, scheduling training sessions and tracking completion of new hire paperwork.
Financial Services industry use cases
- Corporate customer onboarding: Automated customer onboarding can be utilized by financial services institutions to simplify the account opening process. This may include collecting customer information, performing KYC checks and automating the approval and activation of new accounts.
- Employee onboarding: Financial services companies can save time and resources by automating the employee onboarding process. This can involve automating background checks, creating employee profiles in HR systems, organizing training schedules and automating the provisioning of system access.
These are just a few examples of how automation can be applied in the retail and financial services industries to expedite the onboarding of partners, customers and employees.
Automation for financial institutions
Financial institutions can eliminate manual errors, reduce processing time and enhance data accuracy with automated workflows for sharing and signing contracts, agreements, and other legal documents. Furthermore, an integrated ecosystem with automated KYC (Know Your Customer) processes for identify verification and automated fraud detection capabilities can help combat financial crimes and support anti-money laundering (AML) processes.
Supply chain automation
Industrial automation plays a crucial role in today’s manufacturing industry, as it enables the automation of production. IIoT technologies and RPA work synergistically to improve efficiency, productivity and overall operations. IIoT technologies connect physical devices, including edge computing devices, sensors and machinery to a network, enabling them to collect and share data in real time. This data can be used for monitoring, analysis and decision-making. RPA, on the other hand, involves the use of software robots, or “bots,” to automate repetitive tasks and workflows. These bots can mimic human actions, interact with digital systems and perform tasks more quickly and accurately than humans.
When the two are integrated, IIoT and RPA can create a powerful combination. IIoT sensors and devices can collect vast amounts of data about manufacturing processes, equipment performance and supply chain logistics. This data can be fed into RPA systems, which can then use the data to trigger automated actions, such as adjusting process parameters, initiating maintenance requests or optimizing production schedules. The combination of IIoT and RPA can enable predictive maintenance. By continuously monitoring equipment performance through IIoT sensors, potential failures or maintenance needs can be detected in advance. RPA systems can then automatically generate maintenance tickets or schedule repairs, minimizing downtime and optimizing equipment utilization.
With the help of robotic process automation in the automotive industry manufacturing line, manufacturers can automate tasks like the assembly, welding and painting of vehicles. Robots can be programmed to perform repetitive tasks with high precision and efficiency, leading to improved quality, reduced production time and increased cost savings. For example, robotic arms can be used to precisely weld various components of a car body, ensuring consistent quality and eliminating the need for manual labor. This not only speeds up the manufacturing process but also minimizes the risk of errors or defects.
Optimizing supply chain processes and inventory management is another significant automation use case in the automotive industry. Automotive manufacturers deal with a wide range of complex components and parts, making efficient inventory management critical. By implementing automation technologies like barcode scanners and tracking systems, manufacturers can effectively monitor and control inventory levels. Automation facilitates the real-time tracking of parts and materials, matching them with production schedules and automatically reordering parts when stock levels run low. This ensures that the manufacturing process remains uninterrupted, reducing the risk of stock-outs or excess inventory.
Best practices for a successful process automation implementation
Preparing for automation implementation
Throughout the process of developing an automation implementation strategy, always be sure to engage stakeholders and gain buy-in. Successful automation implementation requires the support and collaboration of various stakeholders, including managers, employees and IT teams. Engage them early in the process to address any concerns, and gather their valuable insights. Involving stakeholders from the beginning will increase the chances of a successful automation implementation.
The following best practices can help organizations prepare for a successful automation implementation that enhances security, scales operations efficiently and ensures long-term sustainability:
By following these best practices, businesses can lay a strong foundation for a successful process automation implementation. SEEBURGER can help you scale the future of your business with state-of-the-art integration solutions, including an automation implementation strategy with use cases for your BIS Platform.
How SEEBURGER can help you with process automation
Workflow, task and process automation can be achieved with the strong business process execution language (BPEL) capabilities available in the BIS Platform through a process and workflow engine.
A fundamental characteristic of our platform is that we address users who value configuration over development. This includes the possibility to select a pre-built template from a list of technical and business processes. Following this approach, the selected process is then placed in a chain of actions and requires configuration.
All activities and tasks can be executed either manually via the WebUI or automated via the BIS Platform’s rectification capabilities. Additionally, the export and import of these elements support fast promotion of configuration through multiple landscapes.
The BIS Platform can also integrate into and use automation solution and its functionality through a connector approach. This expands the capability of the BIS platform by allowing it to comply with existing automation solutions in place. BIS offers a comprehensive, robust and built-for-purpose platform that serves this type of automation architecture with integration capabilities, which will complement for example a RPA application or project.
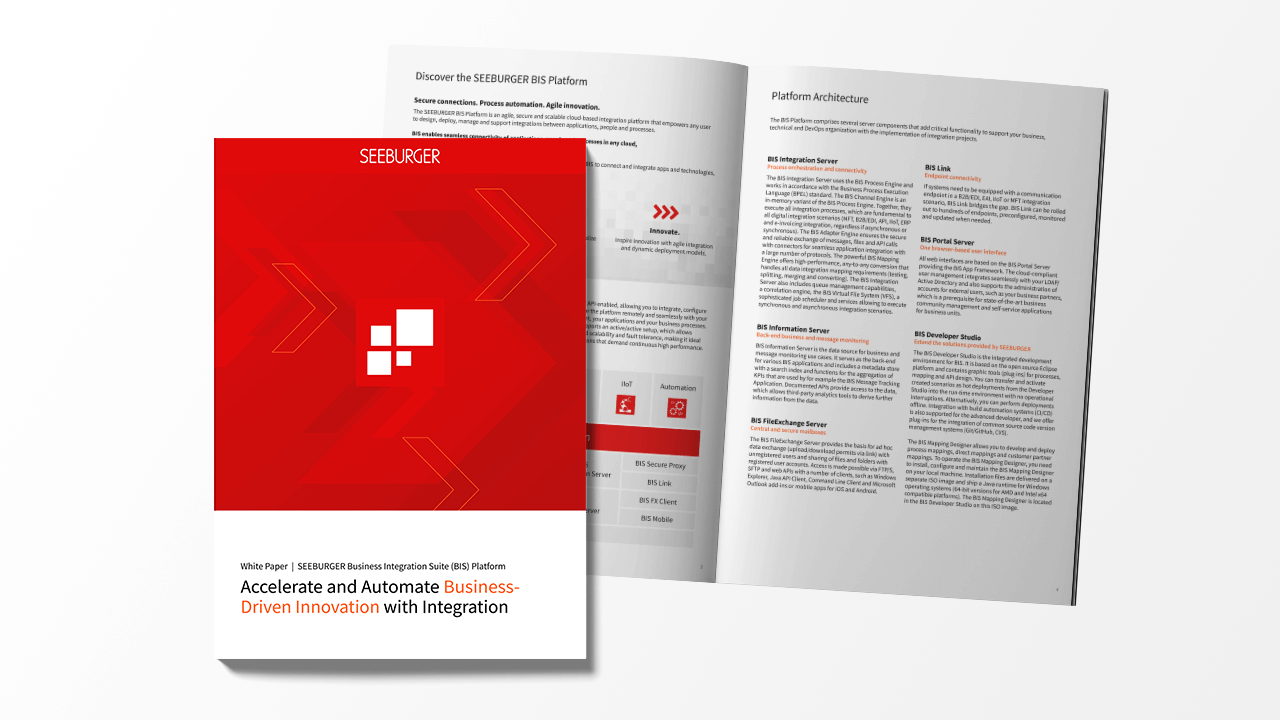
Examples of automation capabilities using the BIS Platform
Expand automation with the BIS Platform
This guide to automation has summarized how organizations can reduce IT effort and costs, increase security, eliminate repetitive manual tasks and accelerate innovation by integrating process automation technologies with their systems, applications, data sources and workflows.
Indeed, the BIS Platform can help drive the expansion of automation in your company as one of the technologies you need in a hyperautomation portfolio 2.
The BIS Platform is our cloud-based integration platform that enables a wide range of use cases and business workflows to be automated with secure, rapid scalability and agile integration capabilities. Deploy the BIS Platform as an iPaaS or with fully managed services in any cloud, a hybrid environment or on-premises.
2 Gartner, “What’s Next After RPA? Hyperautomation: Strategies and Tools for Best Business Outcomes,” Akash Jain, 2023